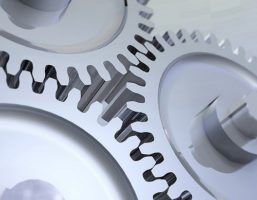
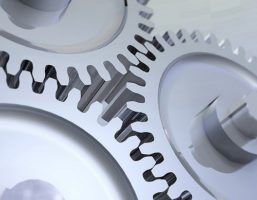
Energy
The Undervalued Role of Wear Materials in Industrial Sustainability
Machines of all shapes and sizes form the iron and steel backbones of businesses around the world. Heavy duty, sophisticated, and above all powerful – these mechanical systems consume an enormous amount of energy over the course of their lives. However, few people consider the other way in which industrial machinery demands resources: during the fabrication and manufacturing processes of building the machines themselves.
Industrial sector companies interested in sustainability ought to factor this “hidden” side of their carbon footprint. That is, the machines they buy are reflective of how they support or don’t support sustainable efforts in other companies.
Rather than dwelling on the sustainability record of the custom fabricators and engineering firms they work with, industries are increasingly opting for a much easier (and cheaper) trick: getting the most out of a single machine rather than replace it with a new one every few years.
The theory is sound. If it takes 20 tons of water, three tons of ore, and however many watts to make a specific piece of machinery when added up, then remove and replace strategies are about as unsustainable as it gets. By using wear technology, making repairs, and performing regular maintenance, factories can extend the lives of their machinery. This, in turn, reduces demand for resource-intensive manufacturing.
The role of wear parts is playing a growing role in this effort with every year. In fact, many industrial components from the first generation of efforts to make energy efficient machinery are already 10 to 20 years old or older. Keeping them running longer and therefore getting the most out of machinery already designed for efficiency, requires wear parts technology.
For many business-minded folks, the sustainability benefits of making a habit of using wear parts technology takes a backseat to the money saving potential. Fair enough. If this proves to be the driving force behind more sustainable business practices, this author approves.
Of course, there are other ways to get extra mileage out of industrial grade machinery. Simple routine maintenance – not unlike the kind performed on an automobile – can prevent wear and tear before it starts. Years of operation can offset gears and bearings by fractions of a millimeter, which won’t be immediately catastrophic but cause damage long term if left unnoticed.
If non-wear parts fail, consult the manufacturer for ways to swap the piece out. Depending on where it’s situated within the works, the replacement can be a simple job. Even complicated projects, when the numbers are added up, are often less costly than total machine replacement.
Speaking of the numbers, if every machine in a factory lasted an extra five years thanks to wear parts replacement, maintenance, and additional parts replacement, it undoubtedly negates the carbon costs of the eventual replacements. Continuing this process for several decades, a single factory following this policy can have a profound impact on the rate in which they ultimately consume resources.
Don’t underestimate the value of wear materials in the matter of industrial sustainability. Keeping machinery operational long past its standard expiration date helps reduce a company’s dependence on environmentally destructive processes. While eco-friendly acts of individuals are important, businesses have an inherently bigger part to play in the fight for more sustainability in this world.
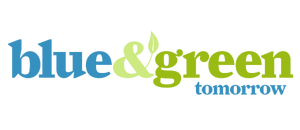