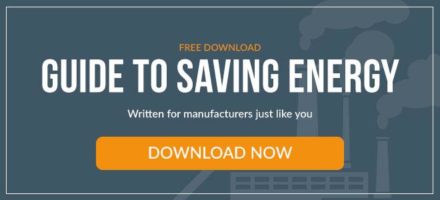
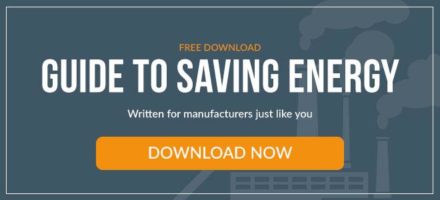
Economy
Taking control of utilities helps manufacturers roll with the punches
A different approach to energy and water consumption could help manufacturers block and evade the combination of punches coming at them this year from forces they can’t control.
UK manufacturers have taken many body blows in the past, but the pressures today are intense. At home, the challenges include skills shortages and political uncertainty over Britain’s possible exit from Europe. On top of this, there’s global competition from overseas firms who pay less for their energy and the demands of keeping pace with environmental and other regulations.
With manufacturing falling around 0.4% from Quarter 1 (Oct to Dec) 2015 to Quarter 4 (Jan to Mar) this year, it’s vital for the UK economy that industry hits back.
One way manufacturers can roll with the punches is to save money and boost profits and competitiveness by taking control of utilities.
Energy is one of the biggest overheads, particularly for those in energy intensive sectors like iron and steel, but it’s a complicated environment requiring good management and planning to meet manufacturers’ energy and water efficiency goals.
At the same time, there are more and more environmental regulations to comply with and pay for. But by participating in initiatives such as climate change agreements (CCAs) manufacturers can achieve energy savings as well as reduced carbon emissions.
Tony Hitchens from Utilitywise, a leader in the utilities field, said: “When companies are able to adapt, they can lessen the force of these pressures. For that, they need expert advice and a strategic energy management plan to give them a joined-up approach to energy and water consumption. This enables them to trim costs, become more efficient and reduce wastage, which could be the difference between profit and loss.”
Manufacturers have the will to make changes, according to a briefing by the Federation of Small Businesses (FSB) but don’t feel empowered to do so because of lack of cash, motivation or information. Nearly 90 per cent of firms questioned wanted to be energy efficient and 86 per cent saw the benefits, but only a fifth said their energy supplier offered energy efficiency advice.
Although the energy market is complex, requiring in-depth knowledge in-house or from external consultants for the best outcome, there are energy efficiencies that manufacturers can achieve relatively easily and independently, with little intervention from outside.
A formal process could be introduced to track and monitor electricity and water usage at each site, for example, or they could introduce good housekeeping and simple investments like these for an immediate impact:
– Repairing cracked windows
– Maintaining furnaces and boilers
– Insulating roofs and walls
– Switching off compressors over weekends
– Installing controls that turn off energy automatically
– Collecting and recycling rainwater
– Turning off fridges when empty
– Fitting a variable speed drive to motors.
Getting the workforce engaged in improvements can pack an unexpected punch. The Carbon Trust estimates that 20 per cent of the energy used to light a site could be saved by simple measures such as encouraging staff to turn off lights when not needed, keeping windows cleaned, opening blinds in daylight hours and reviewing where people are located.
Staff engagement is also vital if manufacturers decide to move manufacturing from times when the National Grid charges more for energy use to cheaper slots. Depending on a manufacturer’s power supply agreement, shifting consumption to different hours of the day can have a large impact on its power bill. But if it affects the workforce, for example by changing tea breaks to different times, people need to know why!
Another way manufacturers can make savings is in procurement – getting the best deal from an energy supplier and ensuring that electricity and gas bills are correct. Energy experts can also check that everything’s being done under carbon change agreements (CCAs) to meet energy efficiency targets and reduce the climate change levy (CCL).
There are also savings to be made by choosing the right contract – fixed price, semi flexible or flexible – at the right time.
Richard Warren, senior energy and environment policy adviser at manufacturers’ organisation EEF, said: “Negotiating your contract at the correct time could save significant sums; wholesale prices can fluctuate as much as 50 per cent during a year. Negotiate a new contract when the price is right, not simply when your current contract is coming to an end.”
Specialists in energy can help industry to make smart decisions in other complex areas of procurement. For example, which contract to choose when companies with 05 to 08 profile class meters reconfigure them to half-hourly (HH) settlement meters next year to meet OFGEM change P272.
When companies change to these meters in April 2017, energy suppliers will offer either a pass-through or all-inclusive contract when they switch. Firms will be billed for exactly what they use but because they can’t manage loads at peak demand it may mean they’re charged more at peak times. To decide which option is best, and the least costly, manufacturers need to understand how they use utilities – and that means monitoring energy and water consumption.
Energy and water data helps to build an intelligent overall picture of consumption, while an energy management plan helps firms understand what they’re using and identify the best ways to reduce consumption and save money.
A web-based utility reporting platform that takes data on water, gas and electricity and creates customisable reports and dashboards allows businesses to see what’s happening with utility consumption and make informed decisions that result in savings.
All of these measures need to be taken as part of an interconnected strategy, which innovations like the Internet of Things (IoT) can help to provide.
“IoT is being explored by industry because it connects digital sensors in key locations in manufacturing sites with people using smartphones and tablets so the machinery in a plant and other equipment talks to each other in a joined up, data-driven way,” said Tony Hitchens.
At the dawn of a new interconnected world, manufacturers will have plenty of opportunities to save on utilities – making them fitter, leaner and stronger to withstand future challenges.
“But even the smallest effort to manage utilities better is always worth doing,” added Tony. “It frees up time to concentrate on business, saves money for investment in the technology needed to keep pace with the competition, and helps to comply with legislation.”
Download the comprehensive manufacturer energy solutions white paper here.
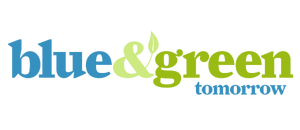
- Economy12 months ago
Sustainable Food Packaging Solutions For a Circular Economy
- Energy10 months ago
The Role of Renewable Energy in Commercial Real Estate
- Economy11 months ago
Why Collaboration is Key for a Sustainable Circular Economy
- Energy10 months ago
How Energy Referral Programs are Saving The Planet… And Your Bank Account!