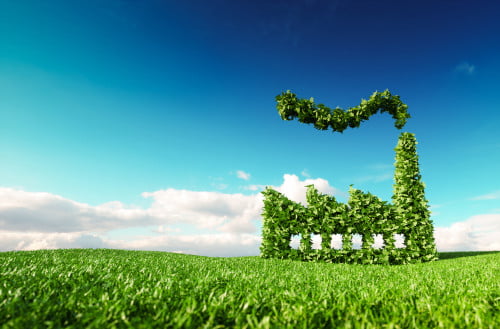
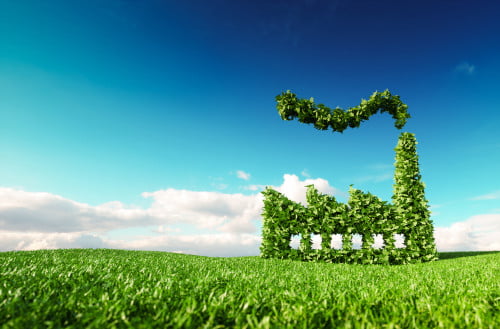
Editors Choice
Tips On Utilizing Green Manufacturing Without Crippling Your ROI
The color green, among other things, represents growth, money, sustainability, and greed. Ironically, the pairs growth/sustainability and money/greed are somewhat contradictory. How so? Well, as we are well into a new year, let’s examine what the hot topics were last year.
Besides politics, climate change and economic growth are back in the news in a good and bad way. As people usually prefer, I will start with the negative. Bad, as in the grim report recently disclosed in the US government’s Fourth National Climate Assessment. It’s a bleak outlook of increasing natural disasters inflicted by Mother Nature for not heeding prior warnings of the dangers that greenhouse gases have on our quality of life and the economy. And, good… as in the rise of American manufacturing and the US economy.
Here’s the first contradiction… We don’t generally equate manufacturing growth with environmental sustainability. Manufacturing conjures visions of dangerous smoke and vapors polluting the air, chemicals leaching into water systems, and plastics floating in our oceans. In order to stop the acceleration of climate change damage, industries need to make changes in their carbon footprint to comply with government and state regulations to become more socially responsible.
Here is where the next contradiction comes in….it takes money to make significant changes in manufacturing processes, and well… greed can prevent more spending. But it doesn’t have to be that way.
So, how can industries make changes and still make a profit to stay sustainable this year and beyond? The answer is making a plan with actionable goals towards implementing green manufacturing practices. This article will explain where to start and how to make environmentally friendly changes in each stage of the product life cycle from design through consumption.
Where to Begin?
The first step is researching State and Federal rules and regulations to make sure your company is compliant. The EPA website provides regulatory information by the manufacturing sector, as well as updates in existing laws or guidelines. Most companies already follow industry requirements, and not doing so can result in fines or imprisonment.
Before a plan can be implemented, a careful analysis of all manufacturing operations in the product life cycle should begin with input from the executive team, production management team, engineering team, maintenance team, buyers, plant supervisor, quality manager. The goal is to find ways to conserve energy, resources, and reduce waste in ways it is economically feasible, and that will ensure long term profitability.
Product Life Cycle
- Design
- Manufacturing Processes
- Packaging
- Transportation
- Consumption
Design
If manufacturers are truly serious about making eco-friendly products, then there is no better place to start than the designing phase. The definition of Design For Manufacturing (DFM) is to make sure that the product is not only easy to manufacture, but also in a cost-effective manner. In this phase, careful consideration should also include what impact this product will have on the environment when its life cycle is over.
A familiar example is plastic water bottles. They are filling up landfills and oceans at a record pace. One company decided to break the mold and create a new business model using locally sourced spring water in a paper container. Just Water containers are 82% paper with a cap made from sugar cane. The results – a 74% reduction in carbon emissions! The risks seem to be paying off as they have introduced a new line of flavored waters.
Manufacturers can no longer ignore the effects of production on the earth or the growing consumer demand for more sustainable products.
What about manufacturers whose products are not biodegradable? How can they still make products that are easy on the environment?
The automotive, electronics, and aerospace industries perfect examples facing this dilemma. Many of these industries use metal components in their electronics systems. With increasing wireless technologies such as 5G, Artificial Intelligence, GPS, computers and satellites, conductive metals are a necessity for proper function. Part of the electronic design phase includes metal selection, and often a few materials share similar properties.
In that case, copper would be a good choice because it has the highest electrical and thermal conductivity making it more energy efficient than other metals, thus lowering operation costs by as much as 20-30%. Copper is easy to recycle and remanufacture because it does not lose its properties. In fact, it is cheaper to recycle than to mine or extract new copper. Copper components are also found in renewable energy systems such as solar, wind, hydro and more.
Manufacturing Processes
Technologies
The operational cost of production is the biggest expense in a manufacturing plant. Thankfully, there are emerging technologies such as Artificial intelligence that is transforming manufacturing by providing real-time data to track machine efficiency and output as well as detecting mechanical failures before they happen.
These machine monitoring systems (MES or Manufacturing Execution System) not only improve production and conserve resources to save money, but they can also prevent mechanical failures. Machine breakdowns are not only costly but can sometimes lead to chemical or gas leaks that can compromise our water supply and atmosphere.
Smart connected factories can monitor many systems within the organization, including utility usage. An investment in this type of technology will lower heating, cooling, electrical and water bills, thus reducing the carbon footprint.
Lighting
Replacing all lighting with LED is an investment in cost savings. In fact, according to research by a London Company that analyzes data for corporations, LED Bulbs Reduced 570 Million Tons Of Carbon Emissions In 2017. To put it into perspective, that is equivalent to closing down 162 coal-fired power plants around the world. Compared to traditional bulbs, LED lights save up to 75% in energy costs and improve employee safety
Solar
Solar energy still remains a viable option to reduce energy costs in factories. Studies have shown that it has become the cheapest energy source in the world. Although, there is debate as to whether solar energy is worth the cost. Savings aren’t seen until long term, and solar panels are expensive, and obviously not effective during night time operations. But, for commercial use it proves to be more cost-effective than residential settings. Larger systems conserve more energy in a shorter time period than residential and the system pays for itself within a few years.
Another incentive is the new investment tax credit (ITC), also known as the federal solar tax credit which allows you to deduct 30 percent of the cost of installing a solar energy system from your federal taxes. Depending on the type of panel, its life span, and the amount of sun, solar energy systems can yield efficiency ratings up to 22%.
Water
Another area that impacts the environment is water usage in daily operations. Ideally, it is beneficial to have a conserve, reuse and recycle plan. The cheapest way to conserve water is preventative maintenance by periodic checks manually or with existing machining monitoring systems. If a capital investment has been made with the latter, it is important to know the lowest volume of water needed to run machines efficiently. Machine monitoring systems provide this data, as well as detect malfunctions which can cause leaks.
Beyond conservation, recycling water for use in more than one process should be considered. For instance, if a rinsing process does not require 100% contaminant-free water, then perhaps it can be used in another rinse cycle.
And finally, finding methods to recycle water in-house, can greatly reduce consumption. There are many ways to filter water for reuse, and some systems can be installed to existing equipment. For example, in 2010 Dr. Pepper’s Snapple plant installed a reject recovery reverse osmosis (RO) system for treated water. This capital investment resulted in over 90% water savings and a huge environmental impact as well as money their pocket.
Packaging
Seeking sustainable packaging options are popular as environmental awareness has increased. It is also becoming more necessary to find other options as some states and cities are banning certain types of materials.
New material options include plant-based plastics, biodegradable peanuts, corrugated bubble wrap, and more recently, mushroom and seaweed! Unfortunately, there is a higher cost involved when switching to these alternatives. Even more, the manufacturing processes of these materials may deplete resources and increase carbon emissions. As a result, you could be paying more for nothing. The Sustainable Packaging Coalition helps manufacturers weigh the costs before choosing the right materials, and in addition, examines the challenges facing different industry sectors.
If you are not quite ready to make the investment, then finding ways to reduce the amount of packaging is a good start. One example is trading styrofoam peanuts for plastic air pillows. Less packaging means less waste.
And finally, at the very least, make sure your company has a recycling plan for all incoming packages from vendors.
Transportation
Transporting goods and services should not be overlooked when making a sustainable plan. A reduction in packaging materials will help lower freight costs. Choosing local vendors whenever possible will help reduce carbon emissions. And, finally, careful planning with logistic software makes it possible for shipping departments and distribution centers to plot out the most cost-effective way to deliver goods. In some cases, it may be more cost-effective to outsource to a third-party logistics provider.
Consumption
Committing to the green manufacturing process is being mindful of the impact that a used product will have on the environment. And for this reason, all manufacturing efforts should go into creating either a biodegradable, reusable, or recyclable product. Packaging should be minimal and contain instructions on how consumers can safely dispose of the product.
Conclusion
As you can see there are a lot of options to consider and it can be overwhelming. Fortunately, there are Sustainability Consultants who can offer suggestions where the biggest impact can be made in the product life cycle with the lowest cost investment. A carefully managed plan can result in savings and a profit if a company promotes its products and its supply chain as environmentally sustainable.
Manufacturers can no longer ignore how their processes negatively impact the environment and how this affects buyer behavior. Companies that implement Green Manufacturing processes now, will most likely have a competitive edge.
Sources: Panjehfouladgaran, Hamidreza. (2012). Environmental Conscious Manufacturing for Sustainable Growth.
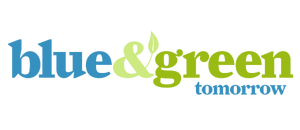
- Economy12 months ago
Sustainable Food Packaging Solutions For a Circular Economy
- Energy10 months ago
The Role of Renewable Energy in Commercial Real Estate
- Economy11 months ago
Why Collaboration is Key for a Sustainable Circular Economy
- Energy10 months ago
How Energy Referral Programs are Saving The Planet… And Your Bank Account!