There are a lot of green living practices that people need to follow. Some of them are a lot more obvious. It is hardly surprising that 90% of Americans support solar energy. Afterall, solar energy has become synonymous with green living.
On the other hand, some green living practices are less obvious. One factor that people often overlook is the benefit of using eco-friendly strategies to save pipelines from corrosion.
Why is protecting pipelines from corrosion an issue that eco-friendly consumers should be aware of? The truth is that there is a huge environmental impact when corroded pipes need to be rehabilitated or replaced. It takes a lot of energy to lift them, solder them and restore them. If the pipes are damaged beyond repair, then there is also the environmental cost of using more natural resources to replace them.
Therefore, protecting pipes from corrosion needs to be a priority.
Preventing Corrosion as a Key Issue in Sustainability
Pipelines are one of the safest ways to transport natural resources over large distances. Between the US and Canada alone, there are just under 5 million kilometres of pipelines spanning the two countries, as part of the large oil and gas industry that contributes significantly to national GDP. Even the safest mode of transportation, however, has its drawbacks and can become susceptible to failure. Corrosion is perhaps the prime culprit behind most pipeline leaks, and occurs when the pipe (typically made of steel) is exposed to water and oxygen throughout its lifecycle. Without preventative measures put into place to protect pipelines from the natural elements, they will corrode, losing their strength and eventually their ability to safely transport raw materials.
To mitigate the effects of natural wear-and-tear, it’s best to implement a series of protection systems that work in conjunction to uphold the structural integrity of the pipeline. Here are three of these best practices.
General Maintenance
Perhaps the most obvious, and overlooked, method to maintaining the health of a system of pipelines is general maintenance. More often than not, the corrosion that inevitably causes pipeline leaks and failures stems from a lack of maintenance of smaller problems that are left unchecked. There are, in fact, a number of maintenance checks and operations that can be performed on a regular basis to ensure the integrity of pipelines. Chief among these include: scrapers, in-line inspection tools and visual surveillance.
The method of scraping uses large wire brushes to essentially scrape the inside of the pipeline, in a rotating motion, to clean the inside of the pipeline and prevent product build-up. A corrosion inhibitor, a chemical compound that —when added to a liquid or gas—works to decrease the rate of corrosion of metal or alloys, may work in tandem with the scraping as an extra precaution.
In-line inspection tools, also known as “smart pigs”, are plunger-like devices equipped with sensors that are inserted into the pipeline and can detect cracks, deformations and metal loss. If any irregularities are found, the sensors will promptly alert the operator who can take action to either repair the affected piece of pipe, or replace it entirely.
Visual surveillance is perhaps the easiest form of maintenance that can be performed, and requires pipeline operators and their employees to walk the pipeline right-of-ways looking for signs of irregularities. These can include: changes in the environment or leaks. Aerial surveillance works in tandem with regular walk-through inspections, and offers a bird’s-eye view to help operators assess the physical integrity of the pipeline across the system, enabling employees to fix or replace any affected parts.
All of these methods of inspection work together to alert operators of any potential problems that can be addressed before disaster strikes. While corrosion is inevitable, the proper care and maintenance of a pipeline will ensure it runs safely and smoothly for decades.
Sealants & Coating
When pipes are installed and buried deep into the ground, they can be extremely difficult to monitor and maintain. Thus, a more holistic approach to pipeline protection is needed. One of the most relied upon methods for protecting buried pipelines is the use of sealants. Some of the earliest iterations of pipeline sealants were made to protect against rust and corrosion, however, newer compounds are made with enhanced capabilities to help protect the pipeline from its surrounding environment. In fact, there are a number of sealant options on the market with different functionalities.
A sealant is a protective coating that’s applied to the surface of a pipeline to protect it from the surrounding elements, including soil and water, as consistent exposure to these (and other) elements will result in corrosion. The most common sealant for underground pipelines is epoxy, which is a paint-like substance that seals the surface of the pipe, keeping natural elements out. If a pipeline is near water, or is a submarine pipeline, the epoxy sealant may be reinforced with cement. While sealants have proven effective in preventing pipeline failure and leaks, their solution is only temporary, because without a way to monitor for weaknesses and irregularities, the pipeline will inevitably fail. This is why sealants and coatings are often seen as a short-term solution that require a long-term, contingency plan.
Cathodic Protection Systems
One of the best preventative measures for long-term defense against pipeline corrosion is the implementation of cathodic protection systems. Cathodic protection is used to control corrosion by using a rectifier to drive the corrosion current away from the pipeline (called the “cathode”) to a sacrificial metal (called the “anode”), which will corrode instead of the pipe. Using these sacrificial anodes, the system is able to detect spots of corrosion before they affect the pipeline, making cathodic protection one of the best methods of preventative maintenance.
Two tests are used to ensure that the pipelines are receiving adequate protection from corrosion: The Test Tap Survey and the Close Interval Survey.
The former involves an operator assessing existing tap test stations along the pipeline, and taking readings. This data will indicate the level of external corrosion mitigation at specific tap test points. The latter involves operators trailing a thin copper wire along the pipeline, connecting it with tap test stations. These readings then indicate whether or not the pipeline is receiving suitable corrosion protection.
Combined with protective coatings, cathodic protection systems are an ideal, long-term investment into protecting pipelines from leaks and failure.
While pipelines are made to last decades, and are one of the best methods for transporting raw materials and natural resources, without proper protection and safety measures, they can and will fail. A combination of general maintenance, protective coatings and the installation of cathodic protection systems will ensure that pipeline systems are protected from leaks that can prove costly to both the operators, and the surrounding environment and communities.
Pipeline Corrosion is a Huge Environmental Issue
Anybody that is serious about protecting the environment needs to make preventing corrosion a top priority. There are a lot of major factors that influence the impact of corrosion and the carbon footprint it creates. The good news is that the steps outlined above can be very effective at preventing it.
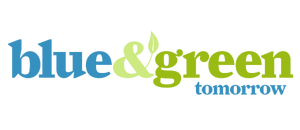
- Economy12 months ago
Sustainable Food Packaging Solutions For a Circular Economy
- Energy10 months ago
The Role of Renewable Energy in Commercial Real Estate
- Economy11 months ago
Why Collaboration is Key for a Sustainable Circular Economy
- Energy10 months ago
How Energy Referral Programs are Saving The Planet… And Your Bank Account!